Spis treści
Dlaczego rdza pojawia się na stali nierdzewnej?
Rdza na stali nierdzewnej pojawia się, gdy jej warstwa ochronna, która zapobiega korozji, zostaje uszkodzona. Głównym winowajcą są zanieczyszczenia powierzchni, szczególnie te związane z żelazem, które potrafią naruszyć tę delikatną osłonę. Zdarzenia takie jak błędy spawalnicze, na przykład źle przygotowany materiał, mogą znacząco osłabić ochronne właściwości stali.
Ekspozycja na substancje żrące, zwłaszcza jony chlorku, bromu i jodu, również wpływa destrukcyjnie na ten materiał. Dodatkowo, warunki atmosferyczne, w tym wilgotne otoczenie czy bliskość morza, zwiększają ryzyko wystąpienia rdzy.
Warto zauważyć, że stal nierdzewna AISI 304 wykazuje mniejszą odporność na korozję w porównaniu do AISI 316, która dzięki dodatkowi molibdenu zyskuje lepsze właściwości w zakresie ochrony przed chlorkami.
Utrzymanie odpowiedniego poziomu czystości powierzchni podczas produkcji oraz użytkowania stali jest kluczowe w walce z rdzewieniem. Zaniedbanie tego aspektu może ułatwić rozwój korozji, co w efekcie prowadzi do uszkodzenia materiału. Dlatego niezwykle istotne jest dbanie o czystość oraz zapewnienie stosownych warunków eksploatacji, aby stal nierdzewna mogła zachować swoje właściwości przez długi czas.
Jakie są mechanizmy korozji w stali nierdzewnej?
Zjawisko korozji stali nierdzewnej jest fascynującym, acz skomplikowanym tematem, który warto zgłębić. Wyróżniamy kilka rodzajów korozji:
- korozja równomierna (ogólna) – polega na równomiernym uszkodzeniu powierzchni metalu na skutek reakcji chemicznych w obecności wilgoci i zanieczyszczeń,
- korozja wżerowa – koncentruje się na lokalnych uszkodzeniach warstwy pasywnej, często związana z obecnością jonów chlorkowych, co prowadzi do powstawania głębokich wgnieceń w materiale,
- korozja szczelinowa – objawia się w miejscach z utrudnionym dostępem tlenu, w których gromadzą się zanieczyszczenia i wilgoć, typowo występująca w połączeniach i szczelinach konstrukcji stalowych,
- korozja międzykrystaliczna – występuje w stalach austenitycznych, ryzyko wzrasta po obróbce cieplnej w określonym zakresie temperatur, wydzielają się węgliki chromu, co obniża odporność na korozję,
- korozja bimetaliczna (galwaniczna) – zachodzi, gdy dwa różne metale mają kontakt w obecności elektrolitu, jeden z metali ulega szybszemu niszczeniu,
- korozja naprężeniowa – pojawia się, gdy stal znajduje się pod działaniem naprężeń w sprzyjających warunkach do rozwoju korozji, co może prowadzić do poważnego osłabienia materiału.
Zrozumienie wszystkich tych mechanizmów jest niezwykle istotne, ponieważ pozwala na lepszą ochronę stali nierdzewnej i skuteczniejszą prewencję przed jej degradacją.
Jakie czynniki wpływają na korozję stali nierdzewnej?
Korozja stali nierdzewnej jest wynikiem wielu czynników, które mogą przyspieszać degradację tego materiału. Jednym z kluczowych elementów jest typ stali, na przykład różne gatunki, takie jak AISI 304 i AISI 316, różnią się poziomem odporności na korozję.
W przypadku stali AISI 316, która zawiera molibden, znacznie lepiej sprawdza się w obecności chlorków, co ma ogromne znaczenie w trudnych warunkach środowiskowych. Dodatkowo, warunki otoczenia, takie jak:
- wysoka wilgotność,
- zmieniające się temperatury,
mogą sprzyjać korozji. Na powierzchni stali zanieczyszczenia, na przykład resztki żelaza, negatywnie wpływają na integralność warstwy pasywnej, co prowadzi do lokalnych uszkodzeń.
Co więcej, błędy podczas spawania czy niewłaściwa obróbka, na przykład zbyt duża chropowatość, prowadzą do powstawania naprężeń, które ułatwiają rozwój korozji. W stalach austenitycznych przegżanie materiału może skutkować korozją międzykrystaliczną.
W takim przypadku dochodzi do wydzielania węglików chromu, co znacząco obniża odporność na korozję. Aby przeciwdziałać tym procesom, regularna pielęgnacja stali, obejmująca czyszczenie oraz kontrolowanie jej powierzchni, jest absolutnie konieczna. Zaniedbanie tych działań może prowadzić do przyspieszenia degradacji stali nierdzewnej, co wiąże się z kosztownymi naprawami oraz koniecznością wymiany materiałów.
Jakie są rodzaje korozji stali nierdzewnej?
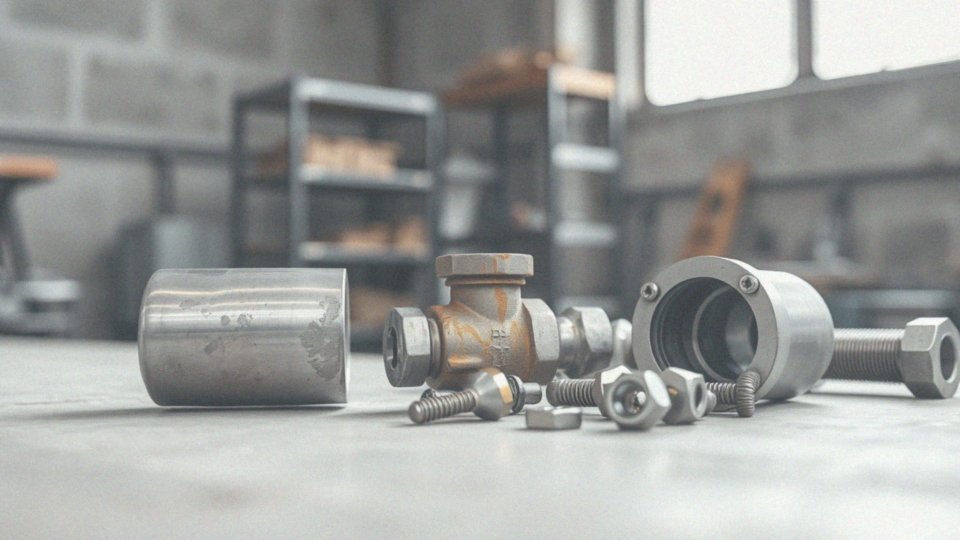
Korozja stali nierdzewnej występuje w różnych formach, z każdą charakteryzującą się odmiennymi mechanizmami, które mogą negatywnie wpływać na jej trwałość. Na przykład, wyróżniamy:
- korozję równomierną, nazywaną także ogólną, prowadzącą do równomiernego uszkodzenia powierzchni metalu, co jest efektem reakcji chemicznych w obecności wilgoci oraz zanieczyszczeń,
- korozję wżerową, koncentrującą się na miejscowych uszkodzeniach, zagrażających integralności materiału, zwłaszcza gdy obecne są jony chlorkowe,
- korozję szczelinową, występującą w sytuacjach, gdzie dostęp tlenu jest ograniczony, co skutkuje intensyfikacją korozji z powodu akumulacji wilgoci i zanieczyszczeń,
- korozję międzykrystaliczną, dotykającą granic ziaren stali, która jest szczególnie prawdopodobna po obróbce cieplnej,
- korozję bimetaliczna, znaną także jako galwaniczną, zachodzącą, gdy dwa różne metale mają bezpośredni kontakt w obecności elektrolitu, co prowadzi do przyspieszonego niszczenia jednego z nich,
- korozję naprężeniową, mającą miejsce, gdy stal jest wystawiona na działanie naprężeń, co sprzyja rozwojowi korozji i może osłabić materiał w poważnym stopniu.
Zrozumienie tych różnorodnych mechanizmów jest niezwykle istotne dla skutecznej ochrony stali nierdzewnej.
Co to jest korozja wżerowa i jak wpływa na stal nierdzewną?
Korozja wżerowa to specyficzny rodzaj korozji, charakteryzujący się tworzeniem niewielkich, aczkolwiek głębokich uszkodzeń na powierzchni stali nierdzewnej. Zwykle uszkodzenia te dotyczą warstwy pasywnej metalu i często są spowodowane przez jony chloru, które mogą przenikać do stali. Te jony występują powszechnie w miejscach, gdzie można spotkać chlorki, takie jak:
- woda morska,
- roztwory soli.
Wżery w stali prowadzą do lokalnego osłabienia materiału, co z kolei zwiększa ryzyko awarii elementów konstrukcyjnych. Pomimo że całkowity ubytek metalu może być stosunkowo niewielki, korozja wżerowa znacząco obniża integralność strukturalną. Długotrwała obecność tego typu uszkodzeń stwarza poważne zagrożenie dla bezpieczeństwa użytkowania. Dlatego, aby ochronić stal nierdzewną przed korozją wżerową, kluczowe jest:
- zabezpieczenie warstwy pasywnej,
- ograniczenie kontaktu z substancjami żrącymi, w tym jonami chloru,
- regularne czyszczenie i monitorowanie powierzchni.
Oprócz tego, zastosowanie odpowiednich materiałów oraz technologii spawania może znacząco zwiększyć odporność stali na korozję. Ważne jest także zrozumienie mechanizmów korozji wżerowej oraz warunków, w jakich ona występuje, ponieważ to kluczowy element ochrony stali nierdzewnej przed niekorzystnym działaniem korozji.
Jak zanieczyszczenia powierzchni wpływają na korozję stali nierdzewnej?
Zanieczyszczenia powierzchniowe mają istotny wpływ na korozję stali nierdzewnej, ponieważ utrudniają tworzenie i zachowanie warstwy pasywnej. Cząstki żelaza, kurz oraz resztki oleju i materiałów powstałych podczas obróbki, na przykład:
- szlifowania,
- cięcia.
Mogą zaburzać proces pasywacji, a w rezultacie ryzyko korozji wzrasta. Problemy z zanieczyszczeniami związanymi z żelazem stają się szczególnie wyraźne. Dzięki nim może wystąpić korozja galwaniczna, do której dochodzi, gdy stal nierdzewna ma kontakt z innymi metalami w obecności elektrolitu. Tego rodzaju warunki prowadzą do preferencyjnego niszczenia jednego z metali. Dodatkowo, korozja szczelinowa intensyfikuje się w miejscach, gdzie ograniczony jest dostęp tlenu. W takich okolicznościach zanieczyszczenia i wilgoć zbierają się, co sprzyja rozwojowi korozji.
Aby skutecznie zapobiegać tym problemom, niezbędne jest:
- regularne czyszczenie stali nierdzewnej,
- pasywacja.
Proces ten pozwala na usunięcie nagromadzonych osadów oraz na odbudowę warstwy pasywnej, co zwiększa odporność na korozję. W przeciwnym razie, zanieczyszczenia mogą znacznie przyspieszyć degradację tego wytrzymałego materiału.
Jakie błędy w spawaniu mogą prowadzić do korozji stali nierdzewnej?
Błędy podczas spawania mogą znacząco zwiększać ryzyko korozji stali nierdzewnej. Do najczęstszych problemów należą:
- nierówne szwy,
- niepełne wtopienia.
Te problemy prowadzą do powstawania miejsc bardziej podatnych na korozję, zarówno wżerową, jak i szczelinową. Pęknięcia w łączeniach negatywnie wpływają na integralność materiału, sprzyjając gromadzeniu się wilgoci i zanieczyszczeń, co przyspiesza proces rdzewienia. Dodatkowo, obecność żużlu po spawaniu ma niekorzystny wpływ na jakość spoin, co może skutkować korozją międzykrystaliczną. Wysoka temperatura spawania prowadzi do wydzielania węglików chromu, które obniżają właściwości antykorozyjne stali. Również brak odpowiedniego gazu osłonowego może przyczyniać się do zanieczyszczenia spoin, co dodatkowo podnosi ryzyko korozji. Użycie niewłaściwych materiałów spawalniczych, które mają mniejszą odporność na rdzewienie, zdecydowanie zwiększa szanse na uszkodzenie konstrukcji stalowej.
Aby zredukować to ryzyko, niezwykle istotne jest:
- zastosowanie sprawdzonych technik spawania,
- regularne czyszczenie spoin,
- dbanie o czystość,
- wybieranie wysokiej jakości materiałów spawalniczych.
Te działania przyczyniają się do długotrwałej ochrony stali nierdzewnej przed korozją.
Jak działa warstwa pasywna na stali nierdzewnej?
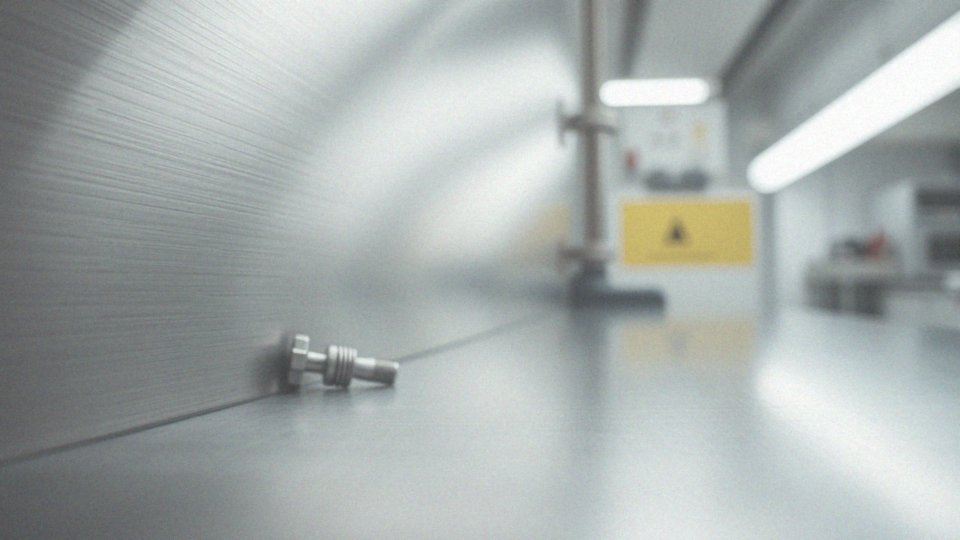
Warstwa pasywna na stali nierdzewnej to cieniutka, ale istotna powłoka tlenku chromu, która tworzy się naturalnie wskutek interakcji metalu z tlenem. Pełni ona funkcję barierową, utrudniając wnikanie szkodliwych czynników, które mogą prowadzić do korozji. Chrom odgrywa kluczową rolę w tym procesie, umożliwiając formowanie i utrzymanie tego ochronnego filmu.
Gdy powłoka pasywna zostaje uszkodzona, na przykład przez zarysowania czy kontakt z chlorkami, ma ona zdolność szybkiej regeneracji, pod warunkiem, że dostępny jest tlen. Te unikalne właściwości przyczyniają się do wysokiej odporności stali nierdzewnej na korozję, co sprawia, że jest powszechnie wykorzystywana w różnych zastosowaniach przemysłowych oraz budowlanych.
Poza tlenkiem chromu, inne składniki stali również odgrywają znaczącą rolę w tworzeniu jej właściwości pasywnych, co jest kluczowe dla efektywnej ochrony. Wybór odpowiednich gatunków stali nierdzewnej, takich jak:
- AISI 304,
- AISI 316.
AISI 316 wzbogacona o molibden zapewnia jeszcze lepszą odporność w trudnych warunkach, typowych dla środowisk z chlorkami. Zrozumienie działania warstwy pasywnej oraz mechanizmów, które umożliwiają jej regenerację, jest bardzo istotne, ponieważ pozwala na zapewnienie długotrwałości stali nierdzewnej i skuteczne zapobieganie problemom związanym z korozją.
Jakie metody pasywacji są skuteczne w ochronie stali nierdzewnej?
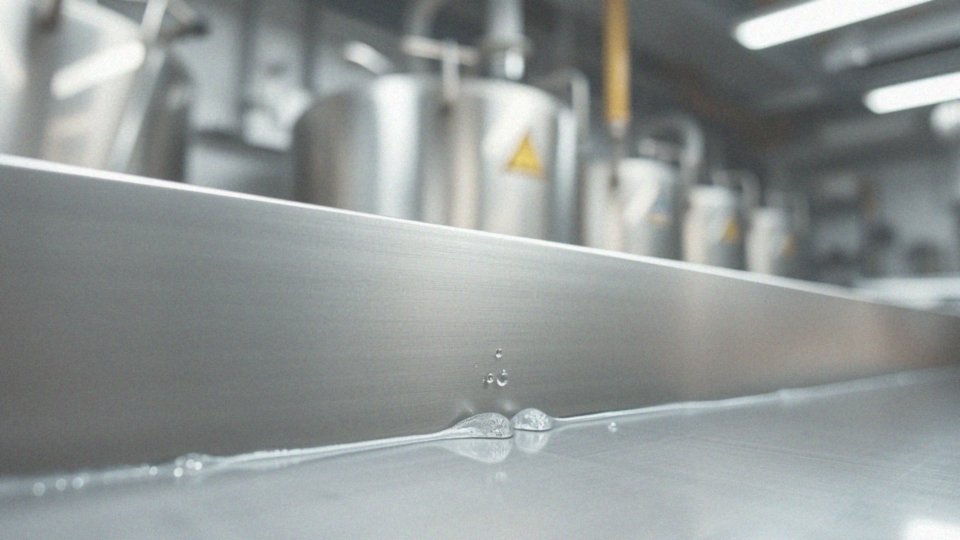
Pasywacja stali nierdzewnej to kluczowy proces, który można przeprowadzać zarówno za pomocą metod chemicznych, jak i elektrochemicznych. Głównym celem tych działań jest odbudowa oraz wzmocnienie ochronnej warstwy na powierzchni stali.
W praktyce często korzysta się z takich substancji jak:
- kwas azotowy,
- kwas cytrynowy,
- kwas fosforowy.
Te substancje skutecznie usuwają zanieczyszczenia, dzięki czemu na stali tworzy się jednorodna warstwa tlenku chromu, stanowiąca istotny element ochrony przed korozją. Innym efektywnym sposobem jest trawienie elektrochemiczne, które wykorzystuje prąd elektryczny w specjalnym elektrolicie do regeneracji wspomnianej warstwy ochronnej.
Po zakończonym procesie pasywacji niezbędne jest dokładne spłukanie stali, aby pozbyć się resztek kwasów, które mogą być szkodliwe dla powierzchni i przyspieszać proces korozji. Aby zapewnić długotrwałą ochronę stali przed rdzewieniem, regularna pasywacja oraz właściwa konserwacja są kluczowe.
Warto również inwestować w wysokiej jakości materiały oraz stosować precyzyjne metody spawania, co ma ogromne znaczenie w kontekście trwałości. Dbałość o czystość powierzchni jest istotnym krokiem, aby zminimalizować ryzyko korozji i wydłużyć żywotność elementów stalowych. Stosowanie odpowiednich metod pasywacji w regularnych odstępach czasu może w znaczący sposób zwiększyć odporność stali na trudne warunki atmosferyczne oraz różne czynniki chemiczne.
Jakie substancje mogą prowadzić do rdzy na stali nierdzewnej?
Różne substancje mogą przyczyniać się do rdzewienia stali nierdzewnej, w tym rozmaite jony i związki chemiczne. Do najistotniejszych z nich należą:
- jony chlorku,
- bromu,
- jodu,
- które występują w soli drogowej i wodzie morskiej.
Kwasy o niskim pH mają zdolność znacznego przyspieszania procesu korozji, szczególnie gdy działają w połączeniu z silnymi detergentami. Długotrwały kontakt materiału ze sporymi ilościami wilgoci zwiększa ryzyko rdzy, szczególnie w sytuacji, gdy na powierzchni obecne są zanieczyszczenia, takie jak cząsteczki żelaza. Używanie narzędzi, które miały wcześniej styczność ze stalą węglową, może dodatkowo zwiększać to ryzyko. Takie zanieczyszczenie może prowadzić do dalszej korozji. Warto też podkreślić, że resztki powstałe w wyniku obróbki, na przykład opiłki metalu, mogą inicjować reakcje korozyjne. Odbierają one skuteczność warstwy pasywnej stali, co negatywnie wpływa na jej właściwości. Dlatego tak istotne jest regularne czyszczenie oraz pasywacja stali nierdzewnej. Dbanie o te elementy znacząco przyczyni się do zwiększenia jej długowieczności i odporności na korozję.
Jak usunąć rdze z powierzchni stali nierdzewnej?
Usuwanie rdzy z powierzchni stali nierdzewnej to proces, który wymaga staranności oraz zastosowania odpowiednich środków czyszczących. Kluczowe jest, aby nie uszkodzić warstwy pasywnej, dzięki której stal zyskuje odporność na korozję. Na początku warto sięgnąć po preparaty zawierające:
- kwas szczawiowy,
- kwas cytrynowy.
Te substancje są zarówno skuteczne, jak i delikatne dla metalu. Najlepszym wyborem do czyszczenia będą gąbki nylonowe lub miękkie ściereczki, które nie naruszą powierzchni. Unikajmy jednak agresywnych środków ściernych, ponieważ mogą one zniszczyć wrażliwą powłokę stali nierdzewnej.
Po zakończeniu usuwania rdzy niezwykle istotne jest dokładne przepłukanie powierzchni czystą wodą, co pozwoli na eliminację resztek używanych preparatów. W przypadku uporczywych plam można sięgnąć po pasty trawiąco-pasywujące. Te produkty nie tylko skutecznie pozbawiają rdzy, ale również przywracają warstwę pasywną stali.
Proces pasywacji jest niezwykle istotny, ponieważ pozwala na odbudowanie ochronnej warstwy tlenku chromu, co zdecydowanie podnosi odporność stali na korozję. Dodatkowo, systematyczne czyszczenie narzędzi oraz elementów stalowych, połączone z odpowiednią konserwacją, znacząco wpływa na wydłużenie ich żywotności oraz minimalizację ryzyka pojawienia się rdzy. Zachowanie tych prostych zasad pomoże w zapewnieniu długotrwałej ochrony przed korozją.
Jak dbać o stal nierdzewną, aby zapobiec rdze?
Aby skutecznie zabezpieczyć stal nierdzewną przed rdzą, warto zastosować kilka istotnych zasad:
- regularne czyszczenie stali za pomocą łagodnych detergentów i ciepłej wody,
- unikanie silnych środków czyszczących oraz narzędzi o działaniu ściernym,
- systematyczne usuwanie zanieczyszczeń,
- pasywacja, czyli regeneracja warstwy tlenku chromu,
- zapewnienie, by stal nie miała długotrwałego kontaktu z wilgocią oraz chlorkami,
- trzymanie stali z dala od innych metali,
- przechowywanie oraz transport w suchych warunkach.
Proste przestrzeganie tych zasad przyczyni się do długotrwałej ochrony stali nierdzewnej przed rdzewieniem i degradacją.
Jak obróbka cieplna wpływa na właściwości stali nierdzewnej?
Obróbka cieplna stali nierdzewnej odgrywa istotną rolę w kształtowaniu jej właściwości mechanicznych oraz zdolności do opierania się korozji. Zróżnicowane techniki, takie jak:
- wyżarzanie,
- hartowanie,
- odpuszczanie,
mają wpływ na twardość, plastyczność oraz strukturę krystaliczną tego materiału. Na przykład, po procesie wyżarzania stal austenityczna zyskuje korzystniejszą plastyczność, co znacznie ułatwia jej dalszą obróbkę. Z kolei stal martenzytyczna wymaga hartowania oraz odpuszczania, co podnosi jej twardość i wytrzymałość na uszkodzenia. Należy jednak pamiętać, że niewłaściwie przeprowadzona obróbka cieplna może zredukować odporność stali na korozję. W przypadku stali austenitycznych, przy określonych temperaturach, może dochodzić do wydzielania węglików chromu. Taki proces prowadzi do korozji międzykrystalicznej oraz osłabienia ochronnej warstwy. Dla przykładu stal AISI 304 jest bardziej narażona na tego typu uszkodzenia niż AISI 316. Dlatego też, odpowiednie metody obróbki cieplnej mogą efektywnie wzmocnić warstwę pasywną stali, co z kolei zwiększa jej odporność na działanie agresywnych czynników. Zrozumienie wpływu obróbki cieplnej na stal nierdzewną jest kluczowe, aby zapewnić jej długotrwałość oraz wytrzymałość w różnych zastosowaniach, zarówno w przemyśle, jak i budownictwie.
Jakie różnice występują między stalą AISI 304 a AISI 316 pod kątem odporności na korozję?
Stale AISI 304 i AISI 316 różnią się głównie pod względem odporności na korozję, co w dużej mierze wynika z ich składu chemicznego. AISI 304, która jest najczęściej używana w wielu branżach, zawiera 18% chromu oraz 8% niklu. W przeciwieństwie do niej, AISI 316 jest wzbogacona w molibden, co zapewnia jej znacznie lepszą odporność na korozję, szczególnie w obecności chloru.
Warto pamiętać, że stal AISI 304 narażona na działanie jonów chlorkowych ma zwiększone ryzyko pojawienia się korozji wżerowej oraz słabą korozję szczelinową. Dzięki molibdenowi, AISI 316 radzi sobie znacznie lepiej z korozją spowodowaną solą, co czyni ten materiał pierwszym wyborem w trudnych warunkach, takich jak:
- środowiska morskie,
- przemysł chemiczny,
- przemysł spożywczy.
Badania pokazują, że AISI 316 może wykazywać odporność na korozję wżerową nawet dziesięciokrotnie lepszą niż AISI 304. Jonowe chlorki, które dostają się do AISI 316, wspierają regenerację jej warstwy pasywnej, co dodatkowo zwiększa jej trwałość w surowych warunkach. W przypadku AISI 304 proces ten postępuje wolniej, co skutkuje szybszą korozją. Ponadto AISI 316 lepiej znosi wysokie temperatury oraz podwyższoną wilgotność, co sprawia, że jest materiałem bardziej wszechstronnym.
Wybór między stalą AISI 304 a AISI 316 powinien być uzależniony od specyficznych potrzeb danego zastosowania oraz otoczenia, w którym stal ma być używana. W sytuacjach, które wymagają wyższej odporności na korozję, szczególnie w zanieczyszczonych atmosferach oraz w obecności wody morskiej, AISI 316 stanowi najlepsze rozwiązanie.